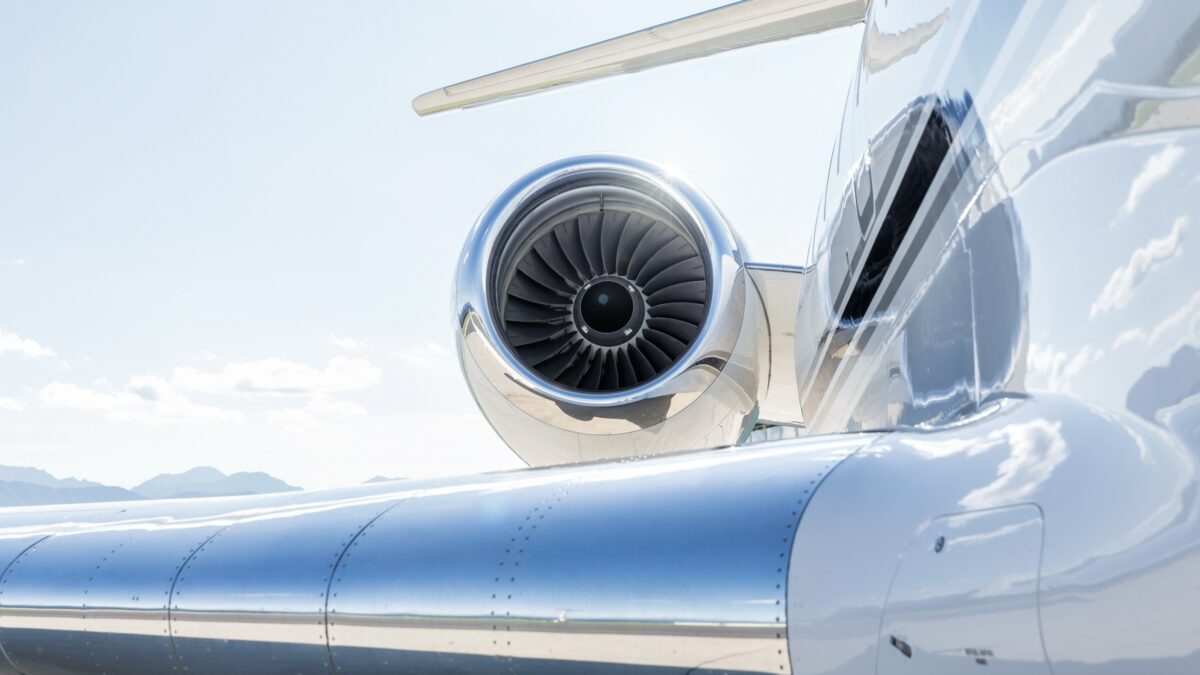
This article is also available in the following languages:
繁體中文
The core of the aircraft is the aero engine, which determines the overall performance of the aircraft. The turbine blades are the key to achieving high performance in a small size and light weight, and are arguably the core of the entire aircraft core.
Introduction to turbine blades
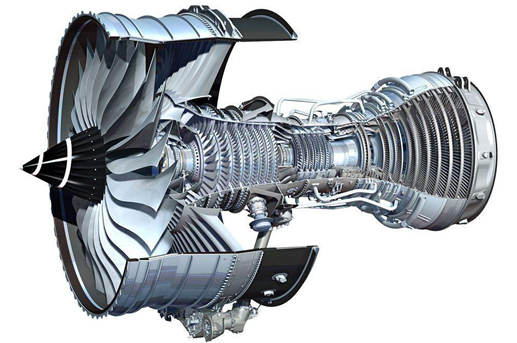
The working environment of the turbine blade is the most severe, and the maximum temperature during working can reach more than 1000℃. Superalloy materials are often used to make blades because of the high operating temperature. While the blade profile is designed to be mainly curved, twisted and swept to better utilize the kinetic energy of the air for heat dissipation.
Turbine blade grinding difficulty point
1.The hardness of the alloy is greater, and it is difficult to process, so a large grinding force and speed is required for polishing. However, this would lead to a rapid shortening of the lifespan of the abrasive belt and an easy change in the location of the consumables.
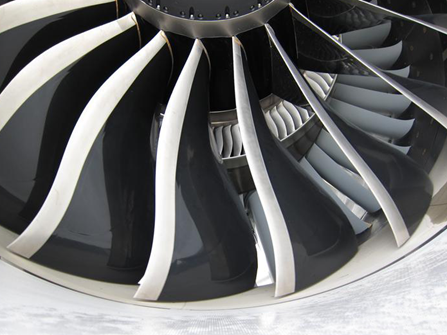
2. Its curved, twisted and swept blade profile design increases grinding difficulty. The surface treatment is smooth and uniform, requiring the robot to be able to point quickly and achieve consistent stability.
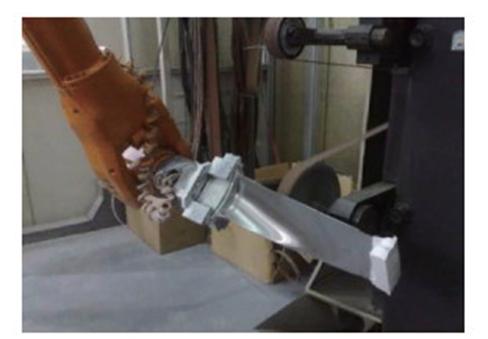
3. The walls of the blade itself are thin. If the grinding margin is small, the cutting force of the machine station is too large and the speed is too quick, or the track of motion is not proper, it is easy to cause the workpiece to wear out or be scrapped.
Polishing scheme
Polishing equipment
Using the unique power of intelligent manipulator and bit-control technology systems, the servo motor dynamically monitors the grinding state and compensates accordingly within milliseconds, enabling self-adjustment of the workpiece size or shape deviation.
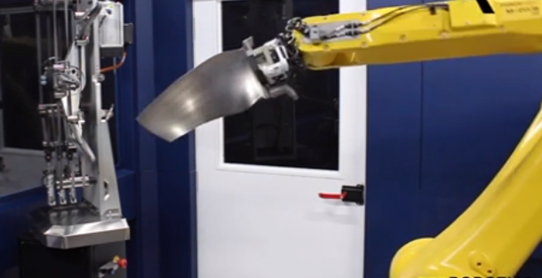
Polishing comsumables
Ceramic abrasive belts are used for both coarse and fine grinding of the blade, while nylon abrasive belts are used for polishing.
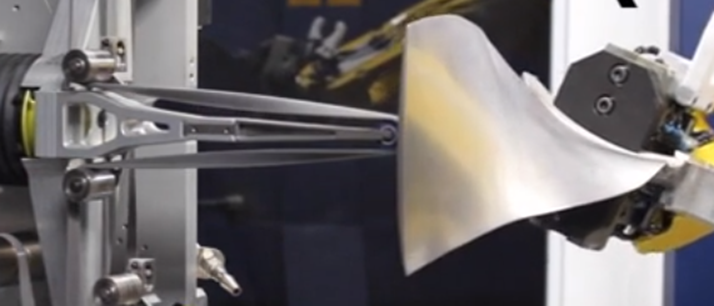