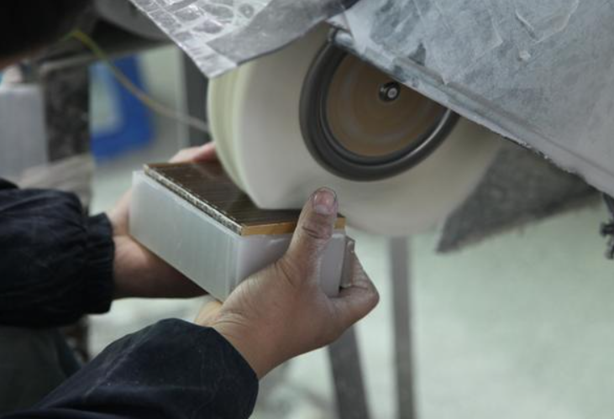
This article is also available in the following languages:
繁體中文
Grinding and polishing is an important part of the good appearance of the product. It can effectively improve the texture of the surface of the product, reduce the surface roughness of the workpiece, improve the finish, enhance the corrosion resistance, and has a very important impact on the quality and performance of the product.
Products of different materials require different methods of grinding and polishing according to different processing requirements. Common polishing techniques are mainly classified into mechanical, chemical, and chemical-mechanical combinations of these three categories, and this paper focuses on several common classifications of mechanical polishing.
Mechanical polishing
Mechanical polishing is the use of flexible polishing tools and abrasive particles to modify the surface of a workpiece and deblend it. Mechanical polishing relies on very fine polishing powders that are ground and rolled to remove an extremely thin layer of metal from the surface of the workpiece.
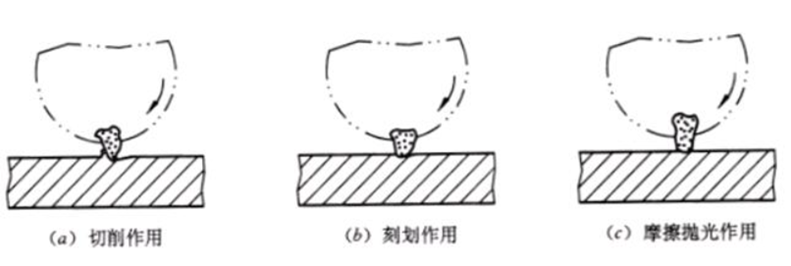
1. Sand blasting
Sandblasting is a polishing deburring process, also known as fluid polishing, which is the process of allowing abrasive particles to flow through certain parts of a piece, deburring, polishing, and rounding the channel surface and corners. It also has a cleaning and lubricating effect, helping to reduce surface friction and prevent overheating. The operation required the use of fluid stirring equipment and special polishing machine equipment.
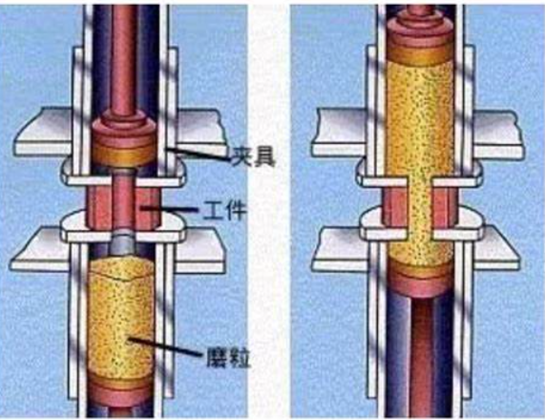
Mainly used for internal orifices, micro-orifices, irregular shapes, spherical surfaces, gears, etc., it is known for its high efficiency, thorough polishing and deblurring, and the absence of damage to the workpiece, but is not suitable for items of particularly large size.
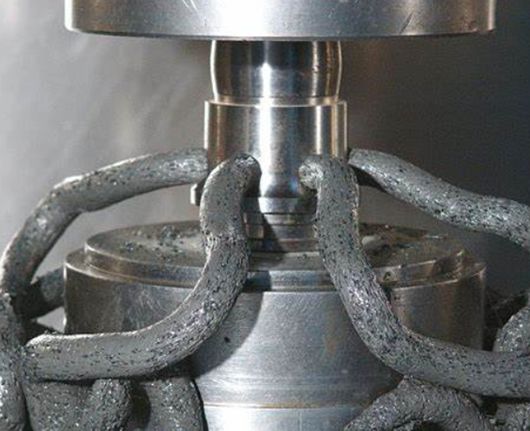
The abrasive particles in the abrasive flow include silicon carbide, alumina, diamond, and other specialized abrasives. Different types of scrubbing, fineness, density, and carrier viscosity can produce different grinding effects.
3. Extrusion polishing
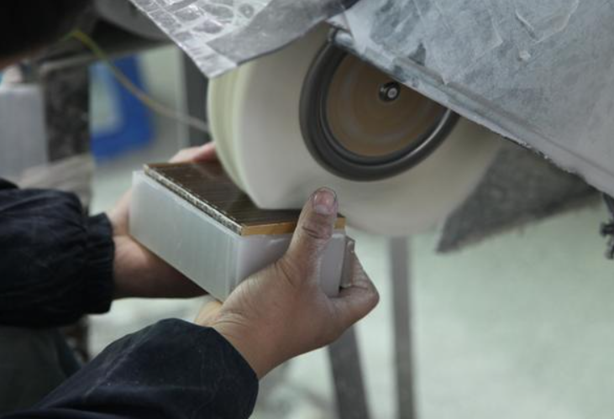
This is a polishing process in which pressure is applied while the workpiece is in contact with the grinding medium, and is commonly used to achieve high accuracy and uniform polish on flat or curved surfaces. Polishing is usually done with a polishing wheel and a polishing paste.
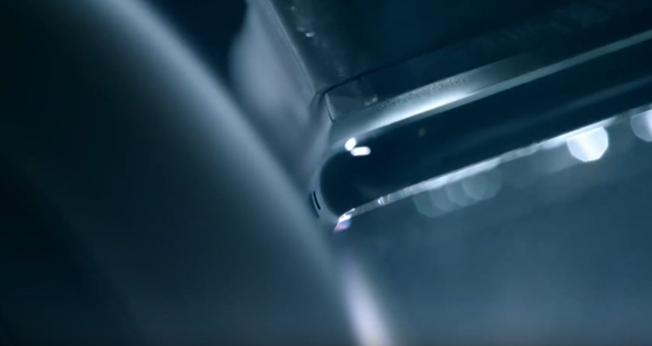
4. Shear Thickening Polishing (STP)
It is a precision machining method for polishing with the help of the non-Newtonian properties of the polishing medium. It has the advantage of high polishing efficiency and good quality.
When the shear strain rate on the slurry exceeds a critical value, the rheological properties of the STP slurry will change and the viscosity of the slurry will rise dramatically, after which it will be transformed into a flexible abrasive tool that can adapt to a variety of surface polishes. The abrasive particles mix with the fluid to form abrasive jets that impact the surface of the workpiece. For the polishing of quartz glass, which is commonly used in optical applications, colloidal silica and colloidal cerium oxide can be used as abrasive particles.
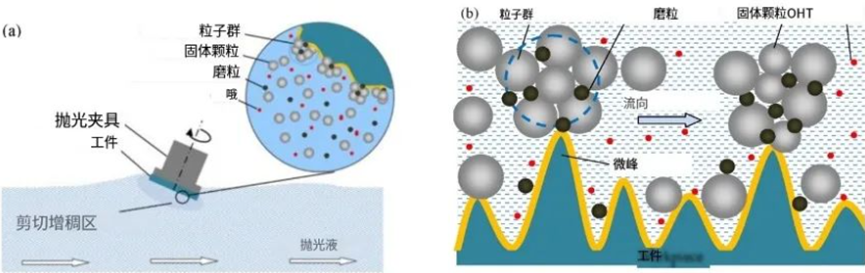
5. Dynamic Friction Polishing
Dynamic Friction Polishing (DFP) is a nano-polishing technique that uses the high-speed movement of abrasive particles on the surface of a workpiece to create friction heat and local pressure to polish and finish the surface of the workpiece. The basic principle of dynamic friction polishing is to generate friction heat and local pressure by bonding abrasive particles to an elastic material and then moving these abrasive particles to the workpiece surface at high speed. The motion of these particles allows efficient polishing at high speeds. Using thermochemical reactions induced by dynamic friction between the diamond and the metal disk, the diamond complex is polished by pressing the diamond complex against the high-speed rotating metal disk at a pre-determined pressure to generate dynamic friction.
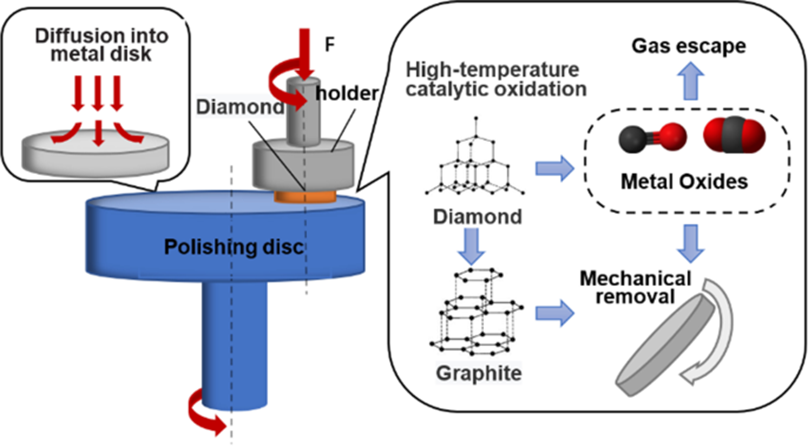
6. Magnetic Fluid Polishing
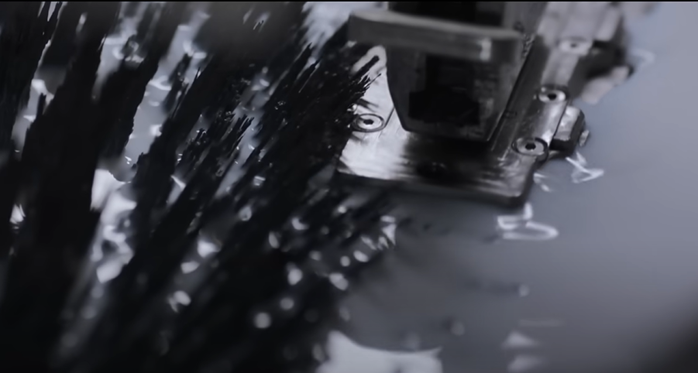
Magnetic Fluid Polishing (MFP) is an advanced machining technique that uses the movement of magnetic particles under a magnetic field to polish the surface of a workpiece.
The basic principle of MFP polishing is to disperse magnetic particles, surfactants, and other additives in a certain proportion in a base fluid to form a method fluid. Under the action of a magnetic field, magnetic particles form chains or fibrous arrangements on the surface of the workpiece, resulting in an increase in the viscosity of the entire fluid, which exhibits solid-like properties. The surface of the workpiece can be polished by the friction motion between the high-speed flowing magnetorheological fluid and the workpiece surface.
The advantages of MFP polishing include high accuracy, high efficiency and low cost. It is suitable for a variety of materials, such as metals, ceramics, glass, etc., and is widely used in microelectronics, optics, machinery and other fields. In addition, MFP polishing can be combined with other processing techniques such as electrolytic polishing, chemical polishing, etc. to obtain better polishing results.
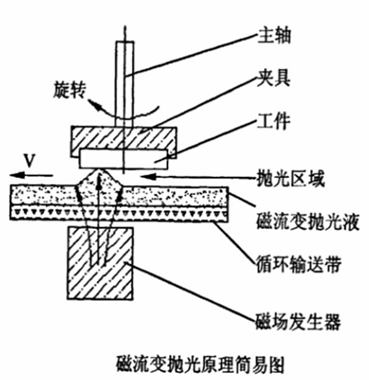
7. Abrasive Particle Eddy Current Polishing
Abrasive Particle Eddy Current Polishing (APECP) is a technique of polishing metal surfaces that uses eddy currents and abrasive particles to polish metal surfaces.
The basic principle of eddy polishing of abrasive particles is to create eddies on the metal surface, which will create a strong magnetic field on the metal surface such that the abrasive particles move at high speed under the magnetic field and polish the metal surface. APECP technology can remove defects of a few microns or approximately 1 wire from the metal surface, enabling rapid grinding and finishing of the metal surface.
APECP technology is suitable for a variety of metal materials such as stainless steel, aluminum, copper, etc. and is widely used in machinery, aviation, chemical industry and other fields. Compared with traditional mechanical and chemical polishing methods, APECP technology has higher processing efficiency and better surface quality, while reducing environmental pollution and waste of resources.
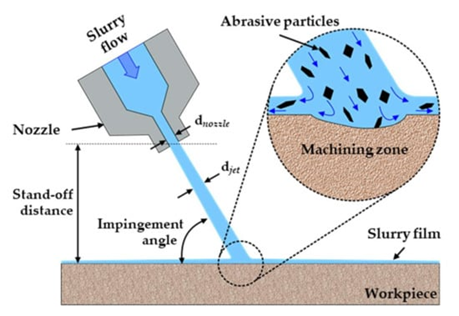