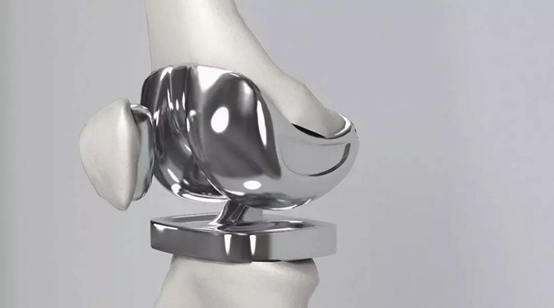
This article is also available in the following languages:
Tiếng Việt
繁體中文
Features of titanium alloys
The types of titanium alloys are roughly divided into three categories: α titanium alloy, β titanium alloy, α+β titanium alloy. At present, the largest titanium alloy specification is TC4 (Ti-6AI-4V), titanium alloy of α+β structure.
Titanium alloys have high strength, good thermal stability, high temperature strength, high chemical activity, low thermal conductivity, higher hardness at higher temperatures, and are one of the most difficult materials to process, with very difficult polishing and poor grinding properties. Grinding titanium alloys usually use a grain size of 36# – 80#.

Problems in the process of grinding
1.The adhesion of the grinding wheels was very serious.
During the grinding process, the titanium alloy on the surface falls off and adheres to the grinding wheel, and the bonded surface falls off together with the abrasive particles on the grinding wheel during the subsequent grinding process, causing very serious damage to the grinding wheel.

2.The workmanship is liable to burn, to deform, to crack.
Due to the higher the temperature of titanium alloy, the higher the hardness of the characteristics, the required grinding force is larger, the temperature is too high, and the heat of the incoming workpiece is difficult to export, its heat will destroy titanium alloy, easy to lead to workpiece burns, deformation, and even cracks.
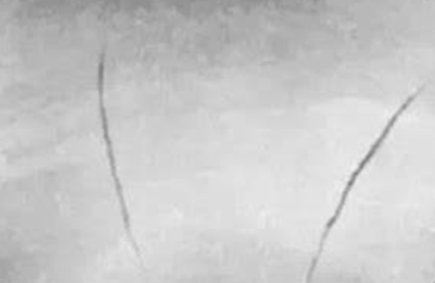
Suitable abrasive
Because titanium alloy is a non-ferrous metal, it is more suitable for silicon carbide (SiC) or green silicon carbide (GreenSiC), or superhard Diamond abrasive (Diamond) to grind.
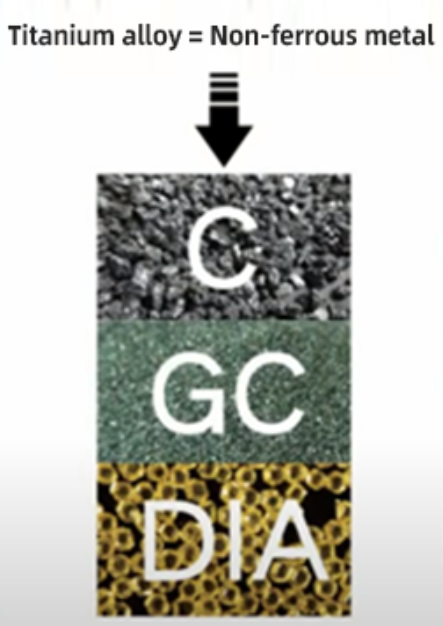
The use of green silicon carbide and silicon carbide grinding wheels is less adhesive and burns and cracks are less frequent. For this reason, green silicon carbide grinding wheels are generally used.

Solutions to the grinding problem
During the grinding of titanium alloy, the grinding wheels bond easily and the workpiece is prone to burn, deform and crack due to the excessive grinding temperature. High grinding temperatures can cause severe plastic deformation, which causes damage to the surface of the workpiece, and can create bonding effects between the abrasive and the metal through physical or chemical adsorption.
The most fundamental solution is to solve the problem of heat dissipation. The common way is to efficiently increase the grinding ratio to achieve more removal with as little grinding wheel loss as possible.
Traditional method
If you slow down the grinding wheel, the grinding temperature will drop as well. Compared to high-speed rotation, better grinding results can be achieved. However, as the speed decelerates, the consumption of grinding wheels will accelerate.
The more time and frequency of dressing, the slower the processing efficiency will be, which also affects its processing cost, and also has a certain impact on the plane precision and dimensional precision of the workpiece, so this is not the best way.
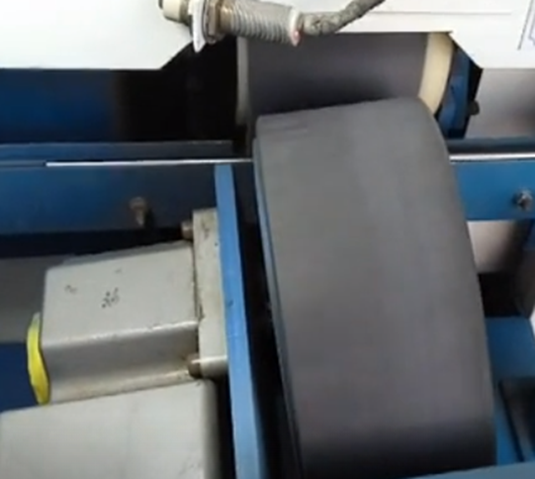
A better approach:
Under constant velocity, good heat dissipation is achieved. In the grinding wheel or grinder can allow the highest speed to do grinding, the use of grinding wheel or grinding fluid or processing conditions, etc., to achieve better heat dissipation effect, as far as possible without losing the rotation speed of the grinding wheel, so as not to cost the grinding wheel.
However, in addition to the cooling and flushing effects, the more important requirement for titanium alloy grinding fluid is to suppress the adhesion and chemical effects of titanium and abrasive particles. Suitable for use with water-soluble grinding fluids containing various extreme pressure additives.
For example, Makeraze LT-623 or Makeraze LT-935 water-soluble grinding fluid, it contains extreme pressure additive grinding fluid, selected additives and unique formulations to ensure its excellent processing performance, and strong lubrication and penetration, can inhibit the occurrence of grinding cracks and adhesion. LT-623 and LT-935 are water-based, environmentally friendly grinding fluids for titanium alloys.
Titanium alloy grinding fluid has excellent biological stability and anti-rust properties. The longest service life can exceed two years. Good anti-rust properties, reducing the consumption of cutting fluid. At the same time, the titanium alloy grinding fluid does not contain chlorine, nitrite, phenol and other harmful substances and is classified as an environmentally friendly grinding fluid that does not irritate the skin and protects the health of the operator.
*Notes on the use of the grinding fluid: When used, it mainly increases the flow rate and pressure of the grinding fluid. The tank capacity should be large enough to keep the grinding fluid at a low temperature. In addition, the temperature of titanium alloy grinding is very high, the chips are flammable and the use of oil grinding fluid requires attention to safety and fire prevention.
If you want to use an existing grinding wheel to improve efficiency, you can try reducing the speed of the grinding wheel to see if the effect is achieved. If you can, this proves that the grinding temperature is a problem, and you can start in this direction to see how other conditions should be set.
In general, the heat dissipation of the grinding wheel is used, coupled with other heat dissipation methods. For example, whether the cut fluid is properly matched to provide better heat dissipation.