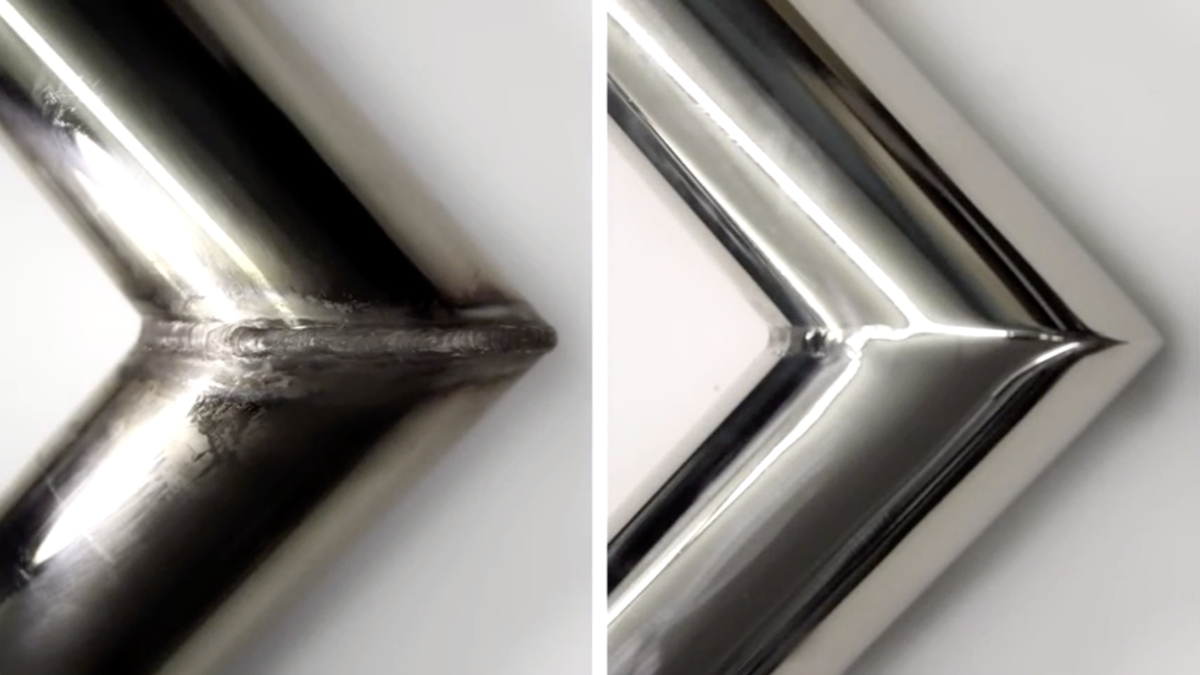
This article is also available in the following languages:
Tiếng Việt
繁體中文
In our daily life, a common combination of metal materials is welding which is efficient and convenience, but it will always present several scars after welding which make the material surface be untidy and ugly.
Someone who wants a perfect beautiful product surface will seek how to remove the welding scars. That’s what we are going to talk about today——How to remove the welding scars fast and well. We have received many customers’ consultation about this question; we will specially focus on removing process of welding scars on stainless steel, to introduce our polishing concept by the following aspects: Types; Relative Hand-held Tool Equipment; Polishing Tools.
And this article will introduce: Polishing for“Vertical Position” Welding Scar of Stainless steel round tube.
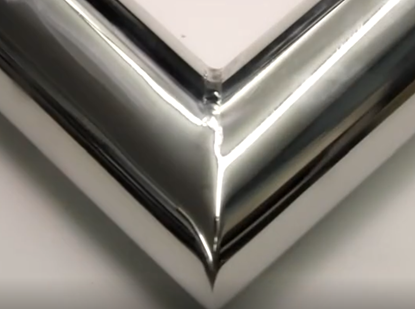
Polishing Equipment
Due to the position of welding part, we usually remove the welding scars by manual polishing, and use hand-held angle grinder.
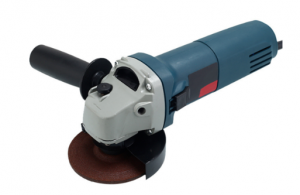
There are a lot of specification of angle grinder on the market; different horsepower, shaft size, connection mode, and different rotate speed (with different polishing consumables size), as well as differences between pneumatic and electric…The commonly used specification abroad is 「4-1/2”x 7/8”」is 114.3mm*22mm (shaft), and in China is 100mm*16mm (shaft).
Polishing Solution Advice
1.Nylon Flap Wheel
Using nylon flap wheel (or called sandcloth wheel) match with angle grinder, to polish smooth the uneven welding scars. Under the high rotating speed of angle grinder, the nylon flap wheel can fast remove the welding scars.
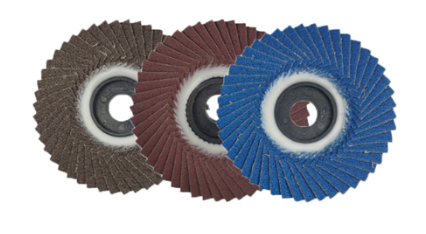
To carry out the operation according to the actual welding scars, we can use #240 nylon flap wheel in the beginning; but if the welding scar area is too large, we can use a rougher wheel first(This step can be omitted if it is not needed); and end with #320, then the welding scars can be smoothed.
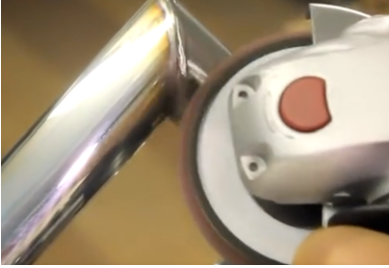
Because the cutting ability and force of flap wheel are quite strong, we must be carefully using it to avoid make irreversible over-grinding to the workpiece.
2.Nylon grinding wheel
The characteristic of nylon grinding wheel has certain softness and its surface covered abrasive particles which make it has certain grinding ability, can effectively remove scratches.
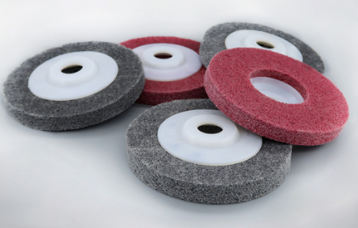
Common suitable specification is “2S Fine”: 2S means 2: Hardness/ S: Silicon/ Fine: about #220~#240; the most suitable rotate speed: 2700-5000RPM (fastest speed had better not exceed 8000RPM to avoid the wheel blow up)
Using grinding wheel match with angle grinder or adhesive nylon pieces match with sanding machine, to polish and smooth the scratches produced at last step.
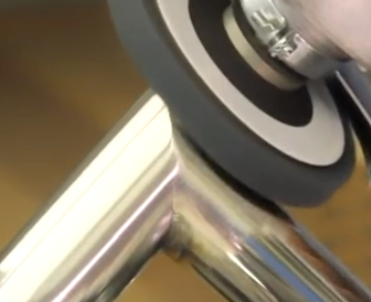
Except the polishing solution of flap wheel +grinding wheel mentioned above, we have a two in one quick solution (as following image show):
Pneumatic hand tool match with 3M spec DF-pro wheel
Spec: 8C: Rough(C/#120)、Middle(M/150~#180) and 2S: Fine (F/#220~#240)
After polishing, the surface can be reached to #320~#400
In this way, we don’t need two kinds of grinding tools and combine the polishing steps mentioned before. But the cost is higher, you can choose the right solution according to your actual requirement.
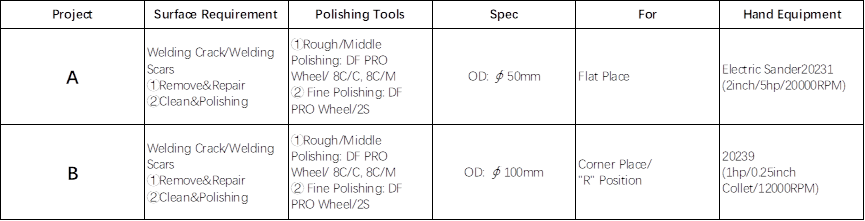
3.Woolen grinding wheel
After sanding to #400, use woolen grinding wheel with angle grinder and our company polishing green wax and white wax; through rough polishing wheel+white wax(Special for Rough polishing) and fine polishing+ fine polishing wax( fine white or green wax), which can quickly polishing the steel surface to mirror surface.
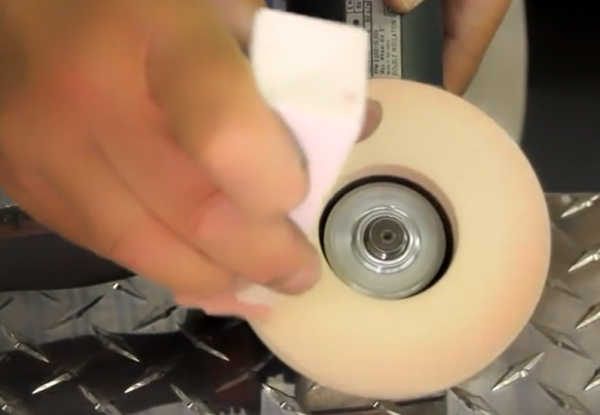
Detail Project:
→DS Sisal Wheel(For Rough Polishing) 150mm*12mm(Thick) *16mm(hole)-GH Treated + SBA-751-2(White wax) →DC cloth Wheel(For Fine Polishing)150mm*12mm(Thick)*16mm(hole) or BC Bias Wheel(For Fine Polishing) 150*16P*16mm(hole) + SBW-084(fine white wax) or SBG-091(fine green wax)
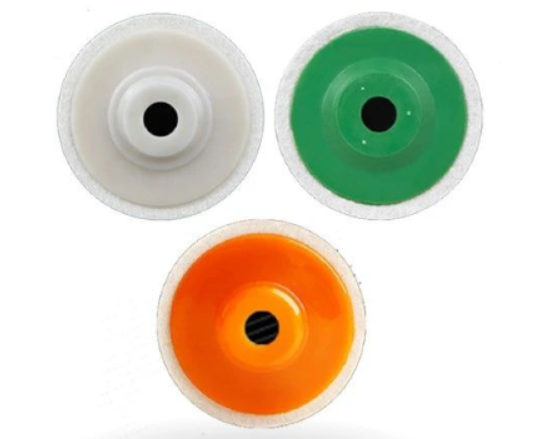
PHYSICAL EFFECTS:
Before
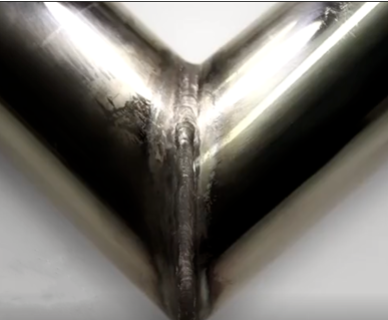
After
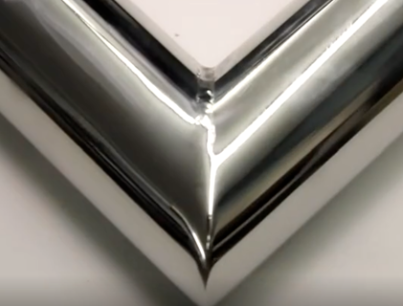