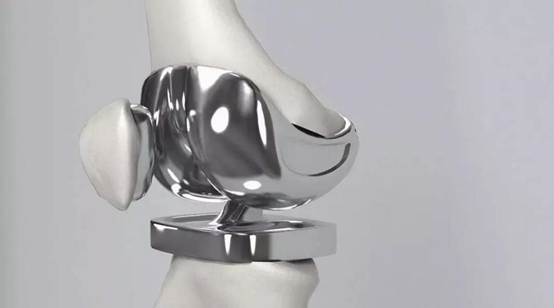
This article is also available in the following languages:
Tiếng Việt
繁體中文
As the population ages, degenerative osteoarthritis has become a common and frequently-occurring disease. As artificial joint technology matures and continues to improve, an increasing number of osteoarthritis patients are opting for artificial joint replacement to relieve pain and restore joint function.
Artificial joints are mainly used in the treatment of joint injuries and loss of joint function caused by joint diseases. Currently, commonly used artificial joint materials include metals, high molecular weight polyethylene, and ceramics.
The metal materials mainly include titanium base alloy (titanium and titanium alloy) and cobalt base alloy (cobalt chromium, cobalt nickel alloy, cobalt chromium molybdenum, etc.).
Titanium alloys are characterized by high strength, low density, non-toxicity, good biocompatibility and corrosion resistance, which are incomparable advantages over other materials. Therefore, titanium and titanium alloy implants have been included in the third category of medical devices and are high-value consumables for use in the medical field.
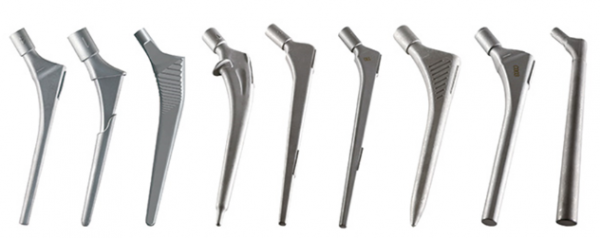
The surface treatment of the artificial joint is very important as it is to be implanted in the body.
Difficult to process
Titanium alloy material is recognized as difficult to process, so titanium alloy polishing because of its wear resistance (low thermal conductivity, small plastic deformation) and poor process performance (work hardening, high affinity with the tool), so in the surface treatment of industrial robots and its software and hardware have higher precision requirements.
Various kinds
There are a wide variety of titanium alloy materials, hundreds of alloys have been developed around the world, with 20 to 30 of the best known, such as Ti-6Al-4V, Ti-5Al-2.5Sn, Ti-2Al-2.5Zr, Ti-32Mo, Ti-Mo-Ni, Ti-Pd, SP-700, Ti-6242, Ti-10-5-3, Ti-1023, BT9, BT20, IMI829, IMI834, etc.
The first practical titanium alloy was the Ti-6Al-4V alloy successfully developed in the United States in 1954. Due to its excellent thermal resistance, strength, plasticity, toughness, formability, solderability, corrosion resistance, and biocompatibility, it has become the dominant alloy in the titanium alloy industry, with the use of this alloy accounting for 75 to 85 percent of all titanium alloys. Many other titanium alloys can be considered as Ti-6Al-4V variants.
In addition, since the 1970s, Ti-Ni, Ti-Ni-Fe, Ti-Ni-Nb and other shape memory alloys have been applied more and more in engineering.
Automatic polishing
1-Polishing machine

With smart manipulators, unique power/bit control technology systems,the servo motor dynamically monitors the grinding state and compensates accordingly within milliseconds to achieve self-adaptation of the workpiece size/shape deviation. The high consistency of the process effects ensures that the uniformity of the cut quantities while maintaining the uniformity of the product quality.
2-Polishing steps
Sanding:
Use special brands and specifications to achieve the best effect (please contact us for more information)
First: 2 “*96” A65
Second: 2 “*96” A30
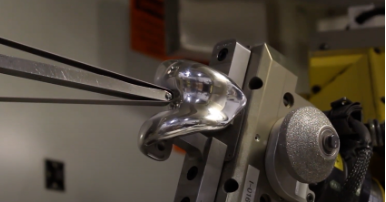
Clear light:
The position of the cloth wheel head is up and down, and the arm holds the workpiece on the wind wheel for second polishing.
First: 18-inch special spec wind wheel + special polishing wax
Second: 18-inch special spec wind wheel + special polishing wax
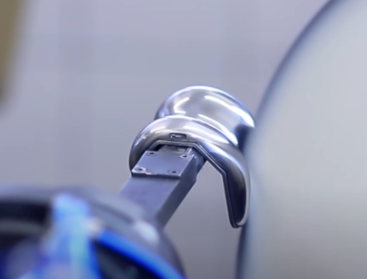
Advantage: Despite use of this machine, the original steps and subsequent steps are greatly altered, such as inspection and repair after polishing. But it is still necessary, because it greatly saves work-hours and technical personnel training, and also improves the working environment (closed).
Hand polishing
The basic process of manual work:There are three parts to be ground, so each should have the following process.
1-Molding
Rough embryos are formed with high-speed grinding wheels.
2-Sanding
Step 1: Sanding – Abrasive Belt #60
Step 2: Sanding – Abrasive Belt #80
Step 3: Sanding – Abrasive Belt #240
Step 4: Sanding – confidential special consumables, please contact us for more information.
3-Polishing
Step 1: Wool wheel (made in Germany)300*25*25(special hardness)+ our special blue wax
With this step, the rear section of the cloth wheel needs only needs to be lightly swept by the flat cloth wheel, and more work hours can be saved.
Step 2: Flat cloth wheel -12″*20P*7/8+ our special blue wax

Our company has extensive experience in polishing techniques and has years of practical experience and testing plans, processes, etc. for workpiece surface treatment. We can customize the best polishing solution for different quality requirements.
If you are interested in detailed specifications of the products required for the specific polishing scheme for the titanium alloy artificial joints mentioned above, please scan the QR code below and contact our customer service for the specific polishing scheme.